The steel story: think zinc on coating line
Journalist Glen Humphries and photographer Sylvia Liber pull back the steel curtain and take you deep inside BlueScope's Port Kembla steelworks
15 June 2016
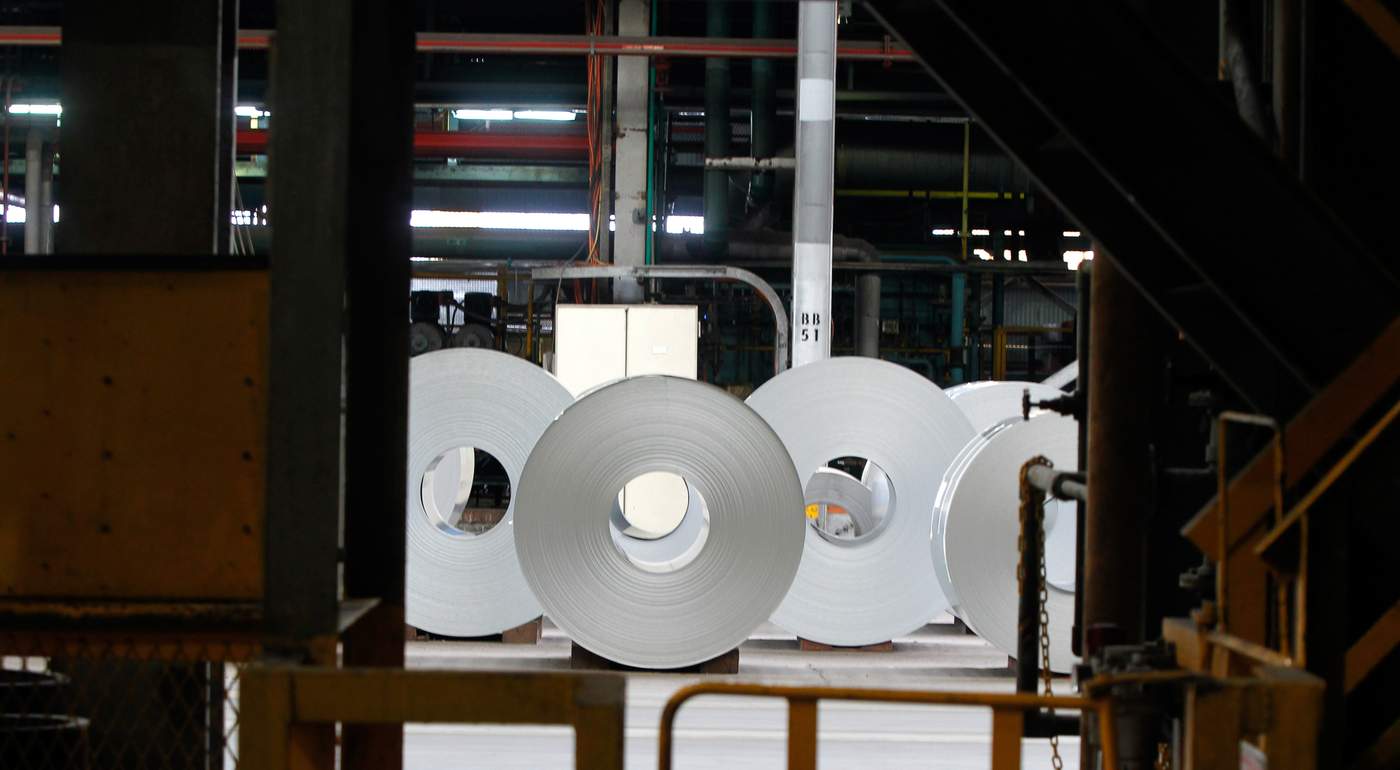
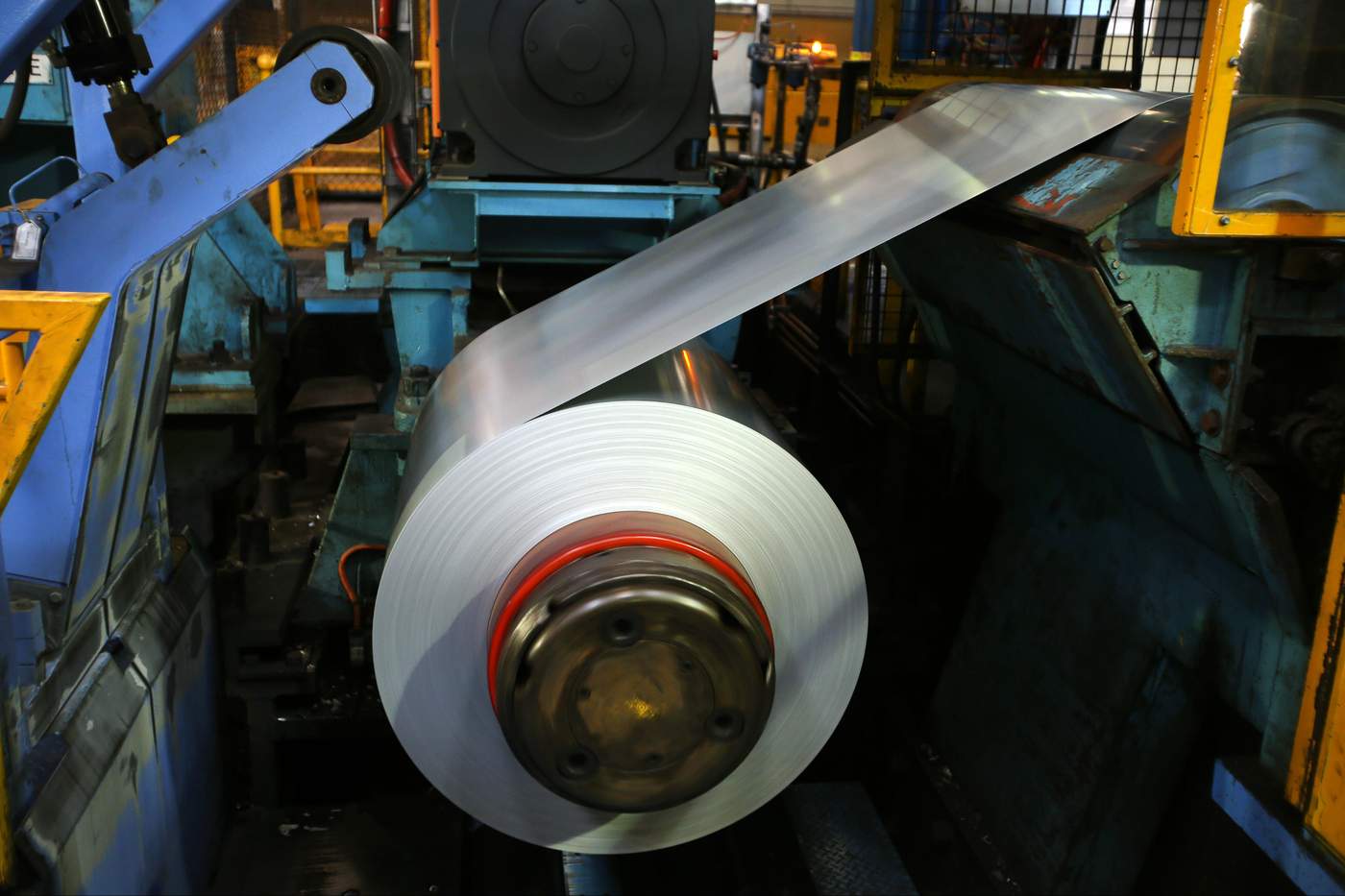
At BlueScope, the closer you get to the end of the line, the cleaner everything becomes.
At the start of the steelmaking process, it’s piles of raw material, dust and steam.
Walk around that for two hours and you feel like you need a shower to get the dust off your skin.
But at the end of the line, where the coating and painting is done, it’s all nice and clean.
Which makes sense - it’s hard to apply a metal coating or paint to something that’s covered in dust.
The penultimate stage in the path of steel through BlueScope is the metal coating lines, where coils are galvanised or coated with a zinc-aluminium alloy.
There are three coating lines - one that does Zincalume, one that does galvanising and a third that can do both.
Combined, the lines coat an average of 850,000 tonnes of steel each year.
It’s also one of the areas at BlueScope where certain things are off-limits in terms of photography, lest some international steelmakers see the photos and get some ideas.
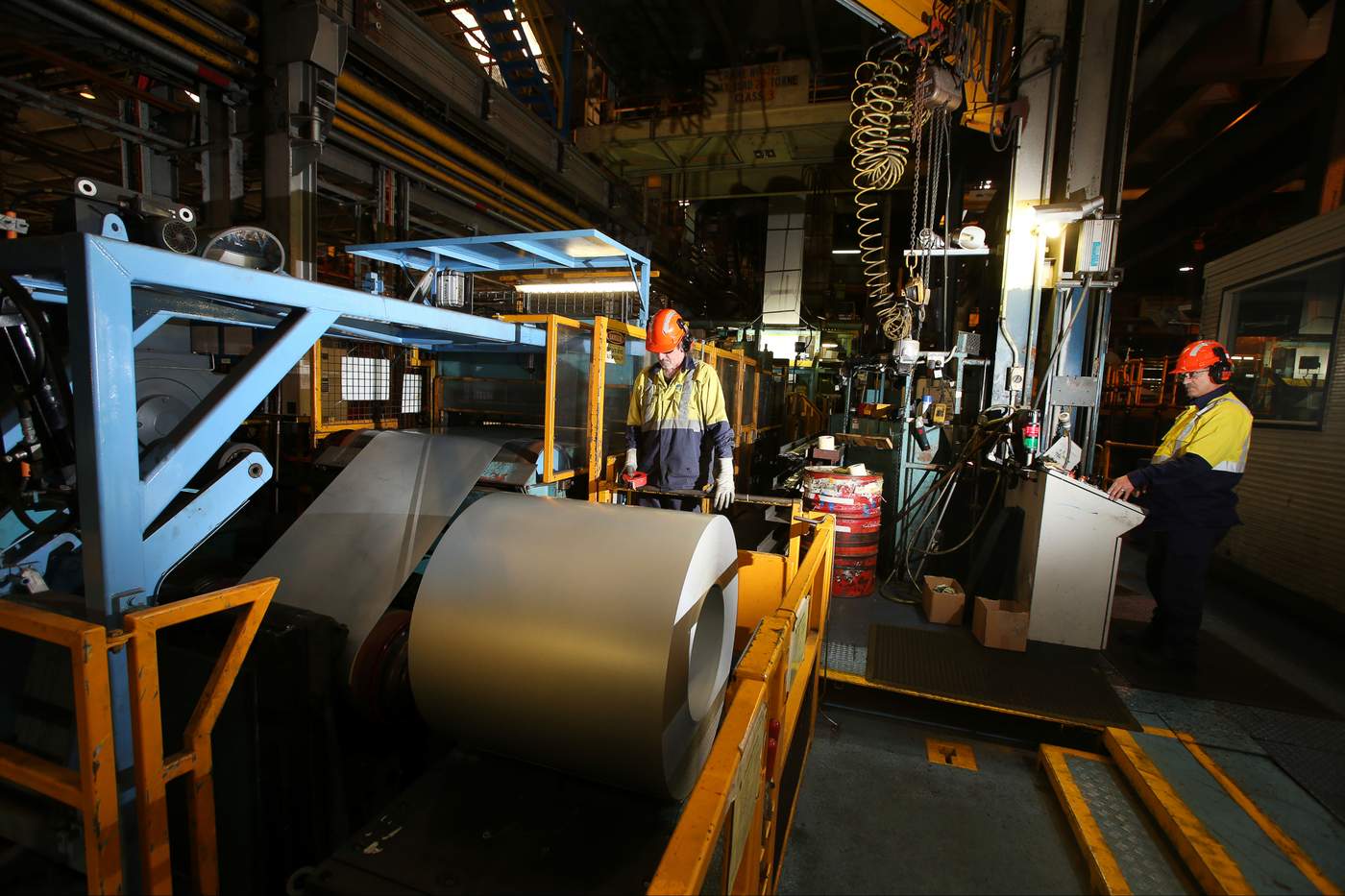
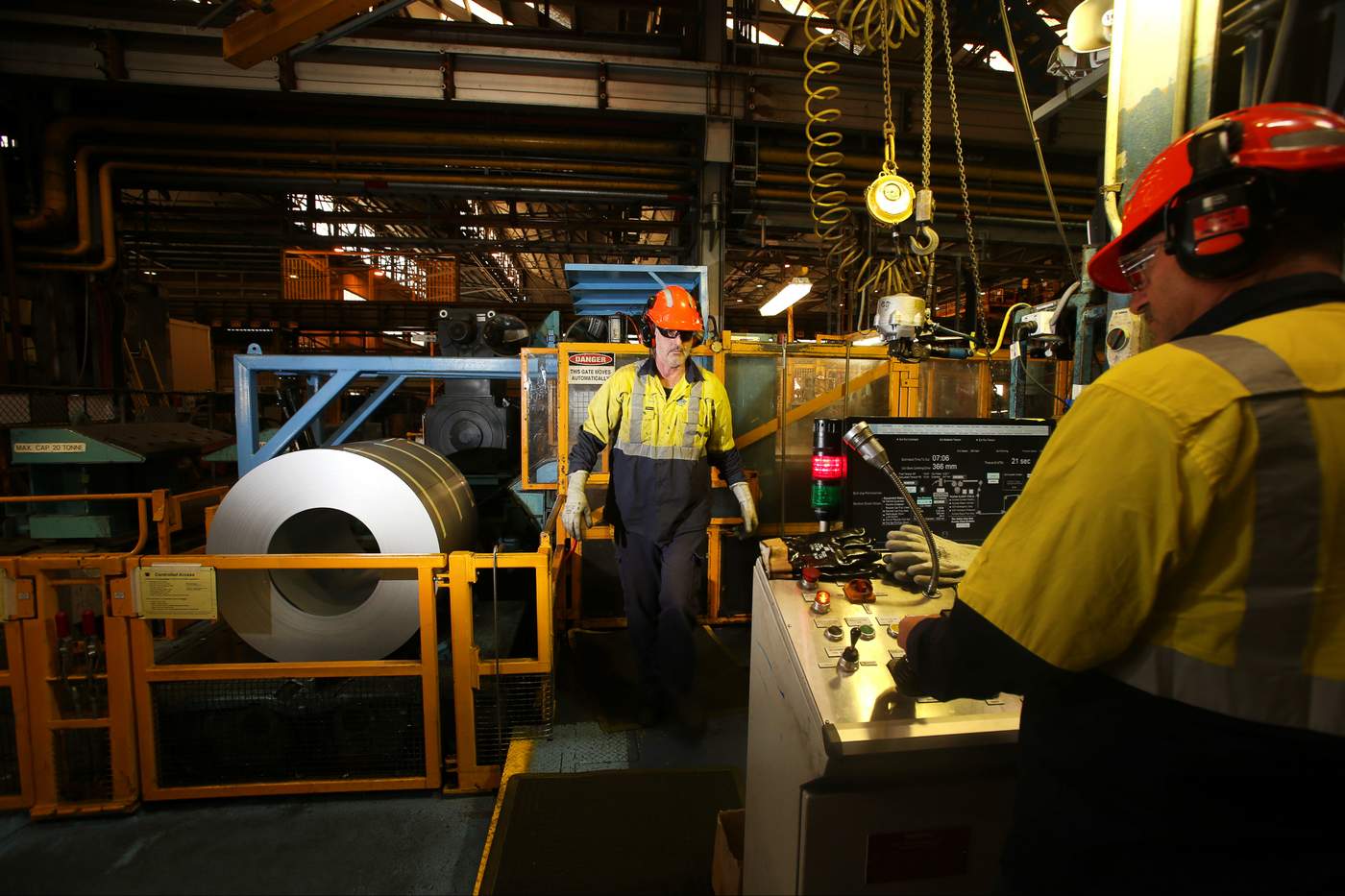
At the start of the process the coils are unwound and welded together in preparation to pass through one of three lines.
The lines do have an accumulator to build up slack to allow it to keep running while the welds are happening.
Like an iceberg most of it is out of sight - the accumulator here stretches underground for eight storeys.
The steel goes into furnaces to get it at the right temperature before getting run through the zinc baths.
Watching the steel run through the baths is a little bit hypnotic.
It runs through vertically and the newly-coated surface is so uniform and perfectly shiny it doesn’t really look like the strip is moving at all.
In fact, you have to look at it really closely before you notice it is actually being pulled upwards through the bath.
It took me a while to realise it was moving - which made me feel more than a little foolish.
From there it’s air and water-cooled and some X-ray testing is done to ensure the thickness of the coating is suitable.
At the end of the metal coating lines, the steel is re-cut with the help of weld-detection technology and - once again - recoiled.
Workers tape up the loose end of the coil and move it out to a stand, where it will be taken out into one of several “coil fields”.
Which field it comes to rest in will depend on what is planned for it.
Some galvanised product heads straight to get packed ready for dispatch, while others - notably those coated with the zinc-aluminium alloy - will get a coating of paint and so has one more step before a customer can pick it up.
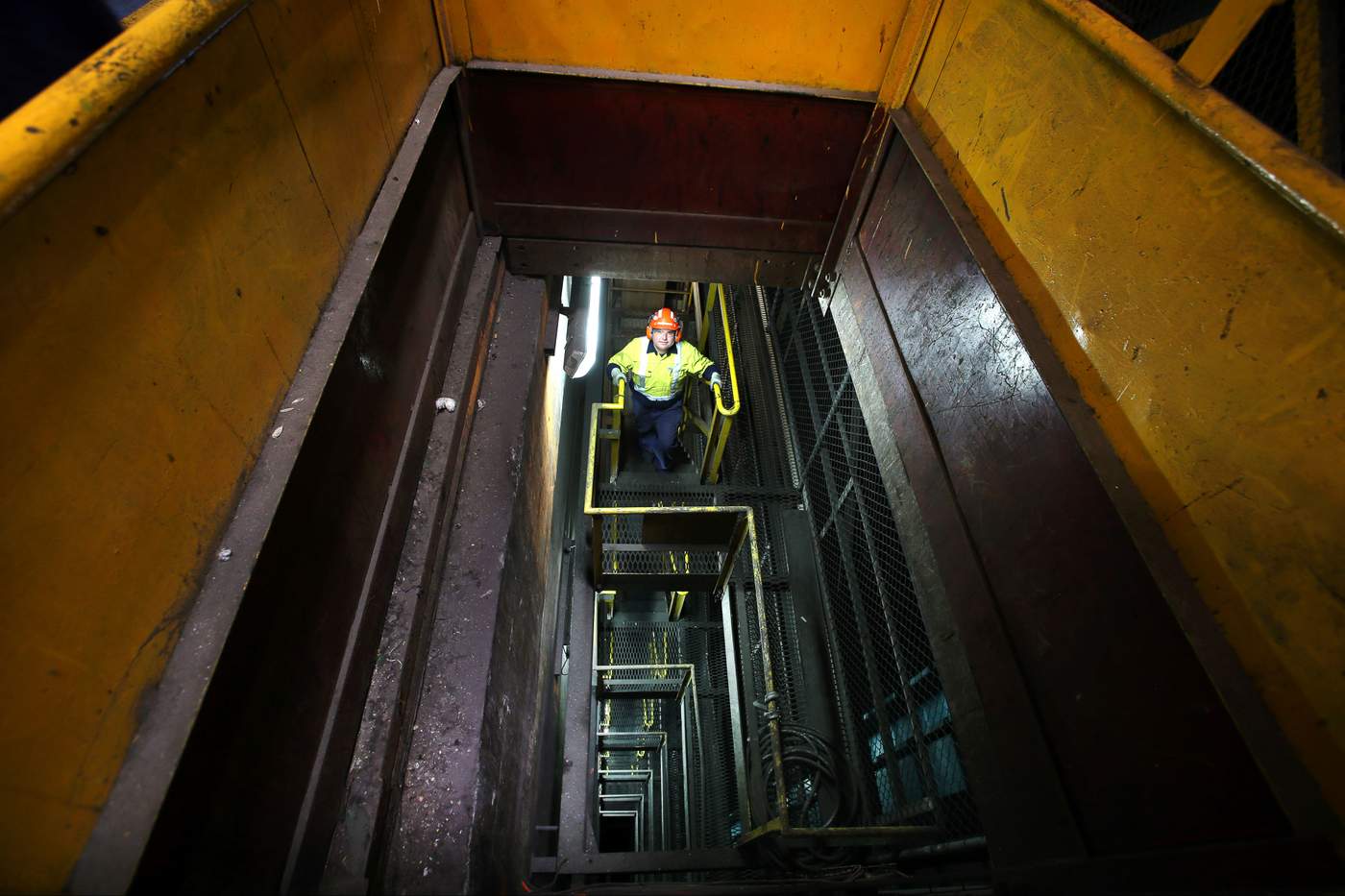
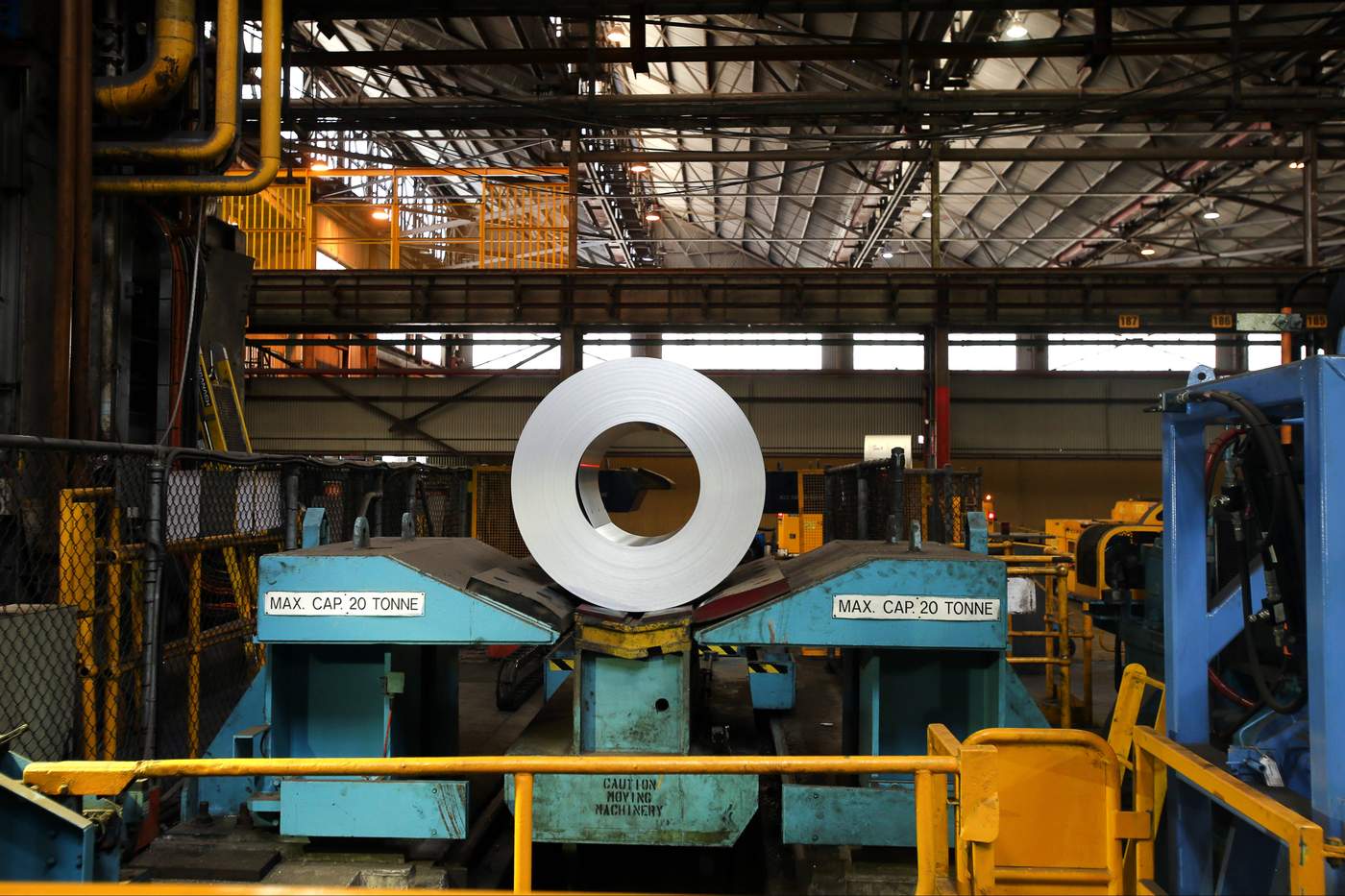
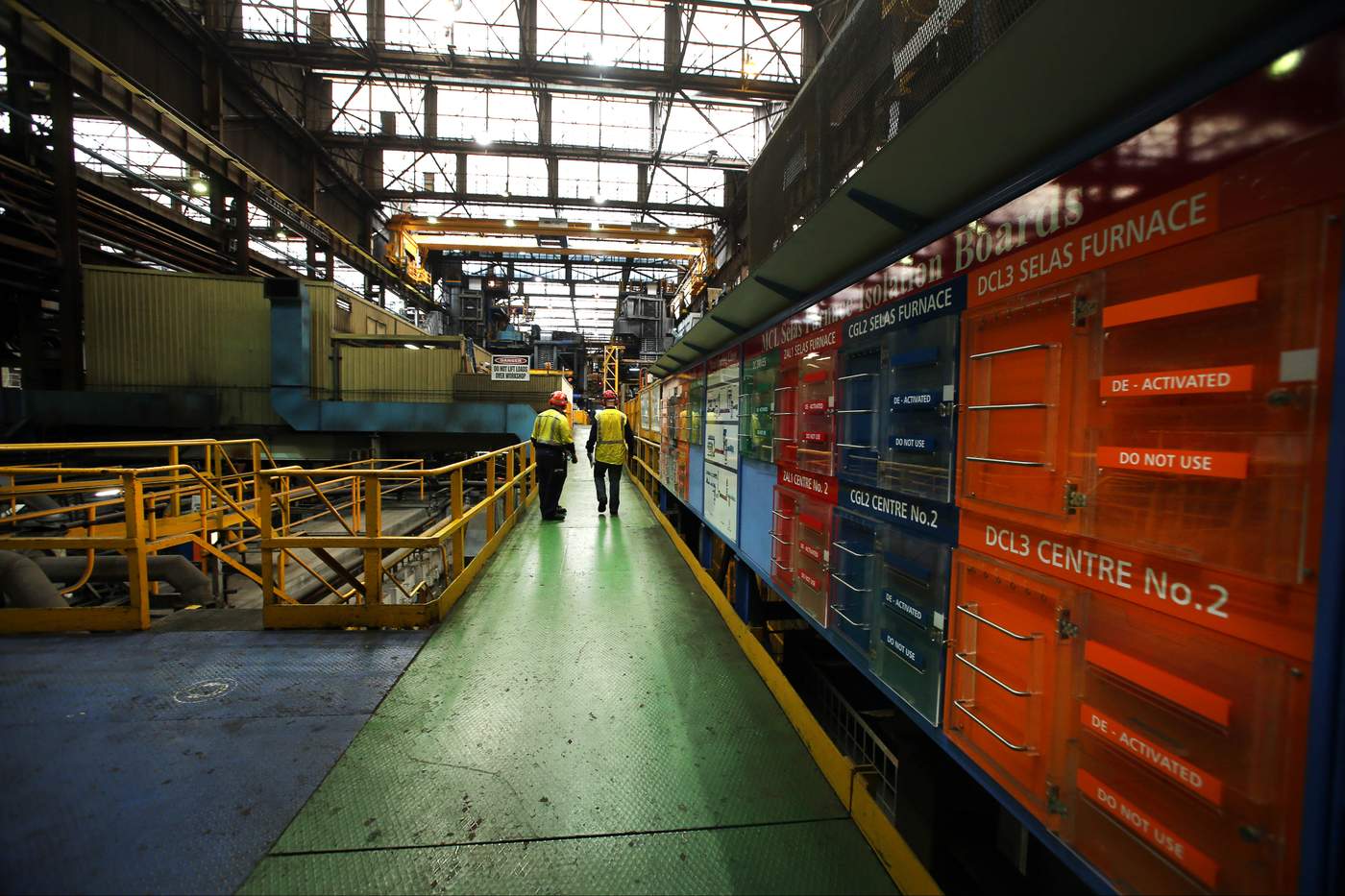